先日、N-ONE用にオークションにて衝動買いした、新しいホイールに履き替えたのですが、履いてみると車高調とホイールのクリアランスが干渉はしていないものの、パッツパツ。
ここのクリアランスに関しては、正直ホイールを回して干渉が無ければ干渉することはありません。
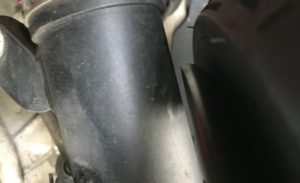
ただ、今回に関してはあまりにも隙間が無さすぎたため、車高調を少々削って分からせてやりましたので、簡単に紹介して行きます。(こんなの邪道だよ。真似しても良いけど自己責任でお願いします。)
車高調とホイールのクリアランス確保のために逃げ加工
先日、購入したホイールをN-ONEに履かせてみると、クリアランスがパッツパツ。正直、ここのクリアランスは歴代の車たちも常にパツパツ状態でしたが、ここまでギリギリなクリアランスになったのは初めてです。
上手くクリアランスがあることが分かる写真を撮るのが無理でした。写真で見ると干渉しているようにも見えますね…。
それもそのはず。シックネスゲージで計測した結果、0.4 〜0.5ミリのクリアランスでした。こんなところにシックネスゲージを使う日が来るとは…。
ホイールを回しても、干渉はしないのでこのまま走行することも可能ですが、何かの拍子に内リムが少しでも波打ったらすぐに干渉してしまうので、保険の意味合いを込めて少々荒っぽいですが、逃げ加工をしてやりました。
削って錆止めの黒を軽く塗装し、完了です。
今回、車高調を削るにあたって、1つの目安にしたのが、車高調に元々ある溝の深さです。下の画像矢印部分。ノギスで、溝の深さを計測し、車高調を削る目安にしています。
削る前にはブラケットの厚みを把握すること…
今回、車高調のブラケットを少々削ってホイールの逃しを作っていますが、もし仮に真似して車高調のブラケットを削るようなことがある場合、削る前にブラケットの厚みがどのぐらいあるか把握しておくことをお勧めします。
※ブラケットの厚みが〇mmなんですけど、どのぐらい削れますか?みたいな質問は絶対にしてこないで下さい。200%回答しません…。
今回は、サンダーで広めの面積を削ってしまっていますが、これからもしやろうとする方は、リューターにてホイールのリムが来る場所をピンポイントで削ってやることをお勧めします。
その方が余計に削ってしまう面積を狭くすることが可能ですね。(面倒なので、サンダーで削りましたが…。)
まとめ
正直、やっておきながらこんなことを言うのもアレですが、車高調のブラケットを削ってホイールの逃しを作る行為はお勧めしません。
ホイールスペーサーを噛ませたり、キャンバー角を起こすなどして他の対策も可能ですので、なるべくならそっちで対処することを強くお勧めします。
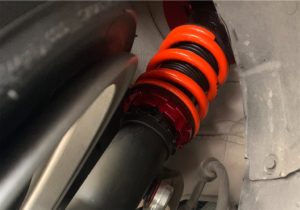
もし真似される場合は、自己責任でお願いします。今回は、ブラケットの肉厚を計測し、ブラケットに元々ある溝と同じぐらいの深さになるよう、ノギスで計測しながら削っています。
それでは。
▪️関連記事はこちら
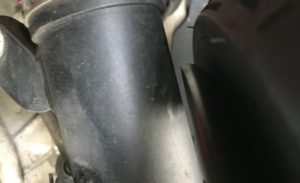
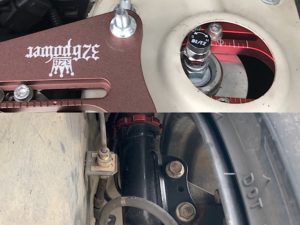
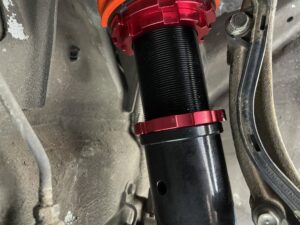