現在製作中のモンキー用にマフラーを購入したのですが、車体に取り付けるとすでにマフラーは着地…。
これでは到底走行は出来ません。(走行するかはさておき)
そんなこんなで、マフラーを底上げするため、エキパイの詰め加工を行いましたので、エキパイの詰め加工について少しお話ししていきます。
使う工具
- グラインダー
- 溶接機
僕が使用している溶接機は100V用のこれ。これを購入すれば、誰でもマフラーの詰め加工が可能です。
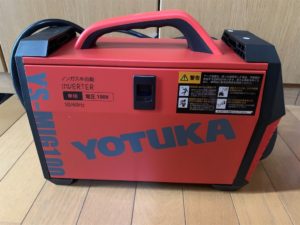
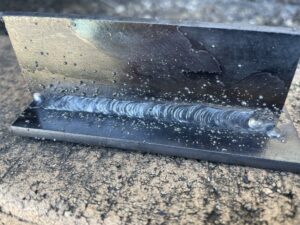
今回加工したエキパイはステンレスではなく鉄ですが、もしステンレスのエキパイを加工する場合は、ステンレス用の溶接ワイヤーを購入すれれば、同じように加工が可能です。
※100Vノンガス溶接は、フラックスワイヤーを購入して下さい。
エキパイの詰め加工/マフラー底上げ
まず始めにエキパイを加工する前の様子を確認しておきます。
少しカメラのアングルが悪いですが、エキパイとクランクケースのクリアランスは、約40ミリほど空いている状況です。
いきなり40ミリカットしてしまうと、角度の補正が出来なくなってしまうので、短縮したい量より少なめの量でエキパイはカットしておきます。今回、1回目のカットは30ミリちょっとで切断しています。
1回目のカットでは、下のマスキングのようにまっすぐエキパイをカットしますが、この後車体に合わせつつ、角度の変えていくので少しづつ斜めに削っていきます。
それにここのクリアランスだけに気を取れれていると、他の箇所が先に干渉してしまう恐れもあります。その辺も注意です。
高速カッターも持っていますが、どのみち角度の補正をするのに削って調整するので、今回はグラインダー1本で切断と削りを行いました。
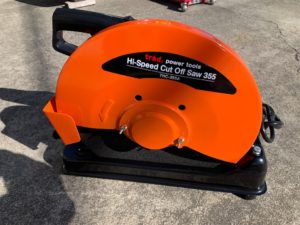
最終的には、4回のカットと角度を補正するための削りを行い、あとは溶接を残すのみの状態まできました。ここに来るまで、何度も車体にマフラーを仮合わせして、削ってをひたすら繰り返し…。
写真で見てもかなり斜切りになっているのが確認出来ますね。
片側を斜めに削って角度補正をするので、多少上下のパイプ径が異なりますが、このぐらいの差であれば溶接可能です。
最後に点付けを行い、マフラーの位置や角度が決まれば1周溶接して作業完了です。
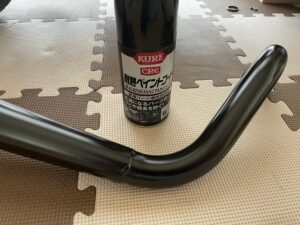
今回、車両の車高がそこまで極端に低いわけでは無いので、クランクケースにぴったりくっつくまで底上げしていませんが、地面とエキパイのクリアランスは、着地状態から45ミリほど確保に成功です。
これ以上上げるとなると、今回のマフラーの場合はサイレンサー側のパイプも角度等を弄らないといけません。エキパイ1箇所だけを詰めて、エキパイが地面と平行になるように加工した結果このぐらいのクリアランスに仕上がりました。
この辺に関しては、使っているマフラーであったり、車両の状態によっても変化するのでやってみないと分からない。と言うのが事実です。
本当にぴったりくっつけたいのであれば、一からエキパイを作成する方法を取った方が楽かもしれません。1号機のダックスは、一から作成しています。
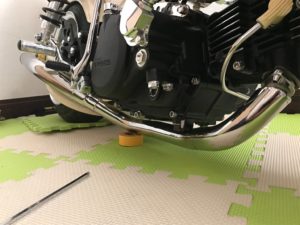
まとめ
見る人が見れば1発で分かるマフラーなのであえて、何のマフラーを加工していたのかは言いませんが…。
新品のマフラーを購入し、開封と同時にエキパイを切断し、クランクケースに近づくようエキパイの詰め加工をしておきました。このぐらいクリアランスがあれば、地面を気にする必要は無いですね。
バンク時のクリアランスも十分確保されているので、バッチリです。
時間と手間は掛かりますが、溶接機さえ購入すれば誰でも出来る作業だと思います。チャレンジしてみて下さい。
それでは。
▪️関連記事はこちら
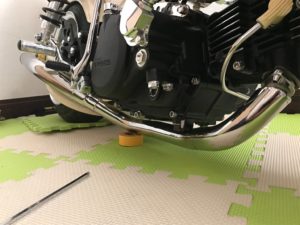
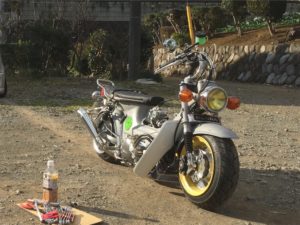
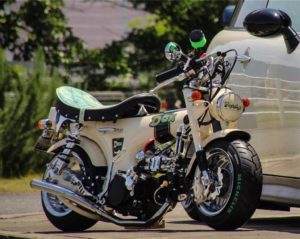
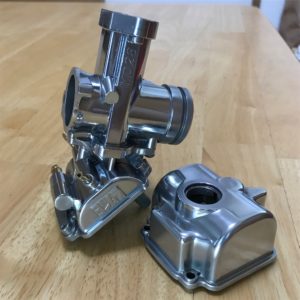
